During the early 2010s, 3D printing captured widespread public attention, particularly in the consumer market, where expectations often exceeded realistic applications. While consumer-grade 3D printing received most of the spotlight, the real advancements were happening in the industrial sector. Behind the scenes, additive manufacturing technologies were steadily evolving—gaining ground in areas such as part accuracy, process reliability, and overall cost-efficiency.
In recent years, significant progress in hardware capabilities, material science, and software integration has dramatically broadened the scope of industrial 3D printing. These improvements have lowered the barrier to entry, making high-performance additive manufacturing accessible to small and medium-sized businesses—not just aerospace or automotive giants.
Today, industrial 3D printers are playing a critical role in accelerating design cycles and reducing manufacturing lead times across a wide range of sectors. These include engineering, production, dental and medical fields, academic research, media and entertainment, jewelry, and hearing aid manufacturing.
When implemented effectively, an industrial-grade 3D printer can transform operational workflows by reducing prototyping costs, minimizing waste, and shortening the path from design to final product. However, selecting the right system requires careful evaluation based on specific business needs.
Overview of Industrial 3D Printing Technologies
Industrial additive manufacturing encompasses several core technologies, each suited to different use cases—from rapid prototyping to end-use part production. Common methods include:
- Fused Deposition Modeling (FDM) – Ideal for functional prototypes and tooling applications.
- Stereolithography (SLA) – Offers high-resolution printing for detailed components.
- Selective Laser Sintering (SLS) – Well-suited for durable, functional parts without support structures.
- Material Jetting – Enables multi-material and color part production with smooth surface finishes.
- Metal 3D Printing – Used for creating strong, complex metal components in industries such as aerospace and medical.
A notable trend across these technologies is the development of smaller, yet highly capable systems. The cost of entry, once in the range of $100,000 to $200,000, has dropped significantly, with systems now available for under $10,000—making industrial 3D printing more attainable than ever before.
Unlocking Industrial Potential with Resin 3D Printers
Resin-based 3D printing has become a cornerstone in industrial manufacturing thanks to its ability to deliver exceptional detail, fine features, and smooth surface finishes that are difficult to achieve with filament-based systems. The use of photopolymer resins opens the door to a wide array of specialized materials engineered for strength, flexibility, temperature resistance, or biocompatibility—making them ideal for industries such as healthcare, engineering, and product design. Whether for functional prototypes or end-use components, resin prints consistently offer superior accuracy and visual quality. Among resin technologies, Stereolithography (SLA) stands out as the most refined, using a focused laser to cure resin with remarkable precision. This layer-by-layer curing process results in parts that meet tight tolerances with minimal post-processing, making SLA a top choice for industrial users demanding professional-grade results.
SLA 3D Printers
SLA (Stereolithography) printers work by using a laser to solidify liquid resin through a process known as photo-polymerization. This method is widely favored by professionals for its ability to produce highly detailed parts with exceptional accuracy and a broad range of compatible resin materials. In the past, SLA was limited to large-scale industrial machines with price tags exceeding $200,000. However, the landscape has shifted significantly. With models like the SUPER MAKER SLA300, businesses can now take advantage of industrial-grade speed and precision in a more compact and cost-effective form.
- SUPER MAKER SLA300: The Super Maker SLA300 is a stereolithography (SLA) 3D printer engineered for high-precision applications. It offers a build volume of 300 × 300 × 300 mm within a compact frame measuring 0.65 × 0.75 × 1.65 meters and weighing approximately 240 kg (excluding materials). The printer utilizes a custom UV laser operating at a wavelength range of 355–380 nm, achieving spot diameters between 0.08 and 0.15 mm. This enables layer thicknesses from 0.05 to 0.15 mm, facilitating detailed and accurate prints. The SLA300 features a vacuum absorption scraper for consistent resin application and a removable, replaceable resin tank for straightforward maintenance. Its scanning speed ranges from 1,500 to 7,000 mm/s, enhancing production efficiency. Designed for user-friendly operation, the printer includes modular integrated circuits for simplified debugging, continuous process monitoring, and overvoltage protection with intelligent high-voltage power-off. Additionally, the 10-inch HD display and self-developed software with customizable functions contribute to an intuitive user experience.
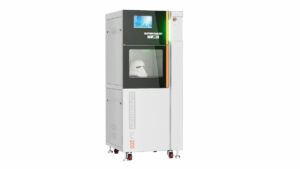
SUPER MAKER SLA300
- SUPER MAKER SLA400: The Super Maker SLA400 is a stereolithography (SLA) 3D printer engineered for high-precision applications, offering a build volume of 400 × 400 × 350 mm. It employs a custom UV laser with a wavelength range of 355–380 nm, enabling layer thicknesses from 0.05 to 0.15 mm for detailed and accurate prints. The printer features a vacuum absorption scraper for consistent resin application and a replaceable resin tank to facilitate maintenance. Its scanning speed ranges between 1,500 and 7,000 mm/s, enhancing production efficiency. Designed with a compact footprint of 0.84 × 0.75 × 1.78 meters and weighing approximately 320 kg (excluding materials), the SLA400 integrates seamlessly into various industrial environments. Additional features include constant temperature and humidity control for optimal printing conditions, a removable mesh plate, modular integrated circuits for simplified debugging, and continuous process monitoring to ensure reliable operation.
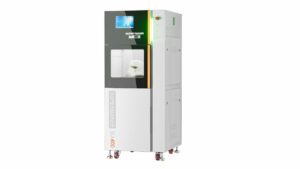
SUPER MAKER SLA400
- SUPER MAKER SLA600: The Super Maker SLA600 is an advanced stereolithography (SLA) 3D printer engineered to deliver high-resolution prints with exceptional surface quality. It features a pulse, UV, all solid-state laser operating at a 355 nm wavelength with a power output of 3W, enabling precise layer thicknesses ranging from 0.05 to 0.2 mm. The printer’s automatic vacuum adsorption coating system ensures consistent resin application, while its substantial material capacity of 180 liters (approximately 225 kg) supports extended printing sessions. Designed for user-friendly operation, the SLA600 includes a removable mesh plate and resin tank, modular integrated circuits for simplified debugging, and continuous process monitoring. Its compact footprint and large build volume make it suitable for producing detailed prototypes and complex geometries across various industries.
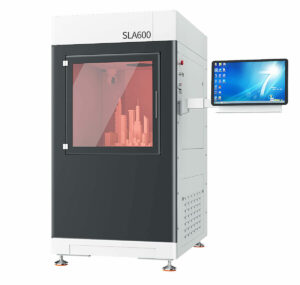
SUPER MAKER SLA600
- SUPER MAKER SLA800: The Super Maker SLA800 is an advanced stereolithography (SLA) 3D printer designed for high-precision, large-scale manufacturing. It features a substantial build volume of 800 × 800 × 500 mm, accommodating sizable components with intricate detail. The printer utilizes a pulse UV solid-state laser with a 355 nm wavelength and 3W power output, enabling layer thicknesses between 0.05 and 0.2 mm for fine resolutions. An automatic vacuum adsorption coating system ensures uniform resin application, while the machine’s robust construction, weighing approximately 1,300 kg (excluding materials), enhances stability during operation. The SLA800 supports SLC file formats and operates on a Windows 7 (32-bit) system with ZH6.0 software. Its Ethernet connectivity facilitates seamless integration into various workflows. Additional features include constant temperature and humidity control, a removable mesh plate and resin tank for easy maintenance, modular integrated circuits for simplified debugging, continuous process monitoring, overvoltage protection with intelligent high-voltage power-off, and a 10-inch HD display for user-friendly operation.
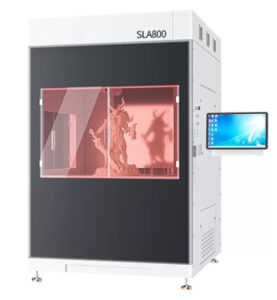
SUPER MAKER SLA800
Advantages of SLA Industrial 3D Printers
SLA 3D printers are known for delivering the finest resolution, exceptional dimensional accuracy, and smooth surface finishes that rival traditional manufacturing techniques. One of the key strengths of SLA technology lies in its adaptability—advanced resin formulations are available to replicate a wide range of mechanical, optical, and thermal characteristics found in industrial-grade thermoplastics.
Compared to other 3D printing methods, SLA is particularly well-suited for producing highly detailed prototypes, precision components, molds, patterns, and even end-use parts. The ability to maintain tight tolerances and achieve clean, professional-grade finishes makes SLA an ideal choice for engineers, designers, and manufacturers. Additionally, its support for specialized resins—including biocompatible options—makes it a go-to solution for medical, dental, and healthcare applications. Models like the SLA400 and SLA800 also offer high-speed scanning systems, enabling significantly faster print times for large-format parts compared to traditional FDM systems.
Disadvantages of SLA Industrial 3D Printers
While SLA offers broad material versatility and exceptional print quality, it typically comes at a higher cost compared to FDM 3D printing. However, it remains more cost-effective than many other industrial 3D printing technologies. One consideration with SLA printing is the need for post-processing steps, which involve rinsing the printed parts to remove excess resin and then curing them under UV light to achieve their final mechanical properties.
Applications of Industrial 3D Printers
Industrial 3D printing has become a game-changer in modern manufacturing, unlocking new possibilities across prototyping, production, tooling, and hybrid manufacturing workflows. With advanced printers, 3D Vector empowers businesses to bring precision, efficiency, and flexibility to their operations.
- Rapid Prototyping: With in-house industrial 3D printers, engineers and designers can transform CAD models into functional prototypes in a matter of hours. This accelerates product development cycles and allows for multiple design iterations based on physical testing and user feedback—without the delays of traditional manufacturing. Additive manufacturing is uniquely suited to prototyping due to its speed, design freedom, and the ability to produce parts that simulate real-world performance, all without the need for expensive tooling.
- Hybrid Manufacturing: By integrating 3D printing with traditional production methods such as injection molding or CNC machining, hybrid manufacturing enables businesses to balance speed and cost with precision and scalability. Whether it’s creating complex inserts for molds, rapid tooling components, or production aids, 3D Vector printers help streamline operations and increase adaptability to changing market demands.
- Tooling, Jigs, and Fixtures: Industrial 3D printing allows for the rapid creation of robust custom tooling solutions that can withstand the demands of the factory floor. Businesses can directly print complex jigs, fixtures, templates, and assembly aids in-house—reducing reliance on external suppliers, cutting lead times, and eliminating the need for minimum order quantities. These parts can be tailored for specific production lines and are easily updated as needs evolve.
- Production-Ready Parts: As additive manufacturing continues to advance in speed and material performance, it’s increasingly being used to produce short-run and end-use parts at scale. Industrial SLA 3D printers offer fine detail and surface quality, making them ideal for manufacturing functional components that meet demanding specifications. From automotive to healthcare, many industries now use 3D printing to produce durable parts, molds, and casting patterns for everyday operations.
- Mass Customization: One of the most powerful advantages of industrial 3D printing is the ability to create custom parts without additional cost or delay. Whether it’s producing patient-specific medical models, tailored consumer products, or custom-fit components, SLA printing makes it easy to scale personalization. With no need for retooling, manufacturers can shift between product variants, opening the door to new business models based on customization.
- Short-Run Manufacturing: 3D printing is perfectly suited for short-run production where traditional methods would require high up-front investment in tooling and setup. Industrial printers from 3D Vector allow companies to economically produce dozens or hundreds of parts with precision, helping validate markets, test new designs, or serve niche demand efficiently.
Get Started with 3D Vector’s Industrial SLA 3D Printers
Today’s industrial SLA printers are faster, more reliable, and more affordable than ever—making it possible for businesses of all sizes to benefit from digital manufacturing. Whether you’re improving product development, streamlining production, or exploring new manufacturing possibilities, 3D Vector offers a range of SLA 3D printers designed to meet your needs.
Get in touch with our team to find the perfect solution for your business and take full advantage of what industrial 3D printing has to offer.