Automotive Industry
3D printing, or additive manufacturing, has revolutionized the manufacturing industry by allowing companies to create complex and customized parts with ease. The automotive industry has been a major adopter of 3D printing technology, using it to produce everything from small car parts to entire vehicle bodies.
One of the main advantages of 3D printing automotive parts is the ability to create complex geometries that are impossible or expensive to produce using traditional manufacturing techniques. With 3D printing, automotive engineers can design intricate parts with complex curves and internal structures, allowing for optimal performance and efficiency. Additionally, 3D printing allows for quick prototyping, enabling designers to test and refine their designs before committing to expensive tooling.
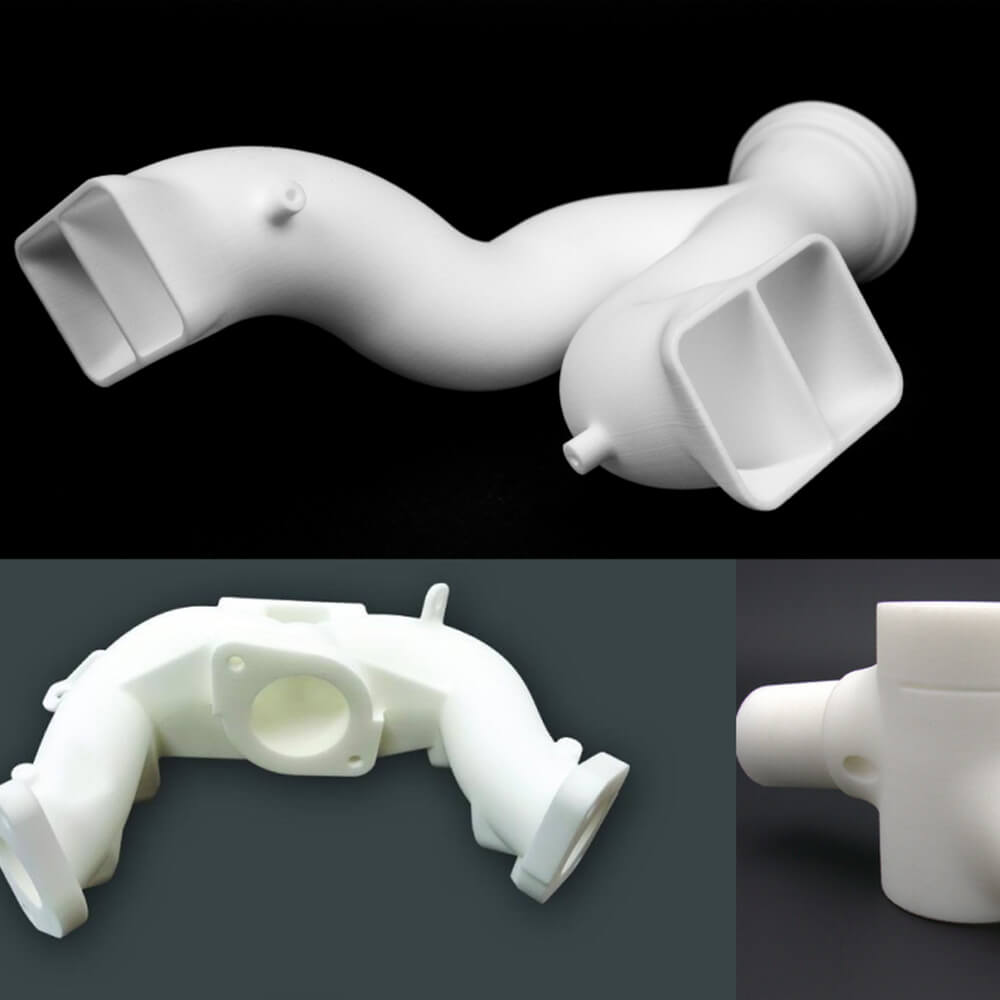
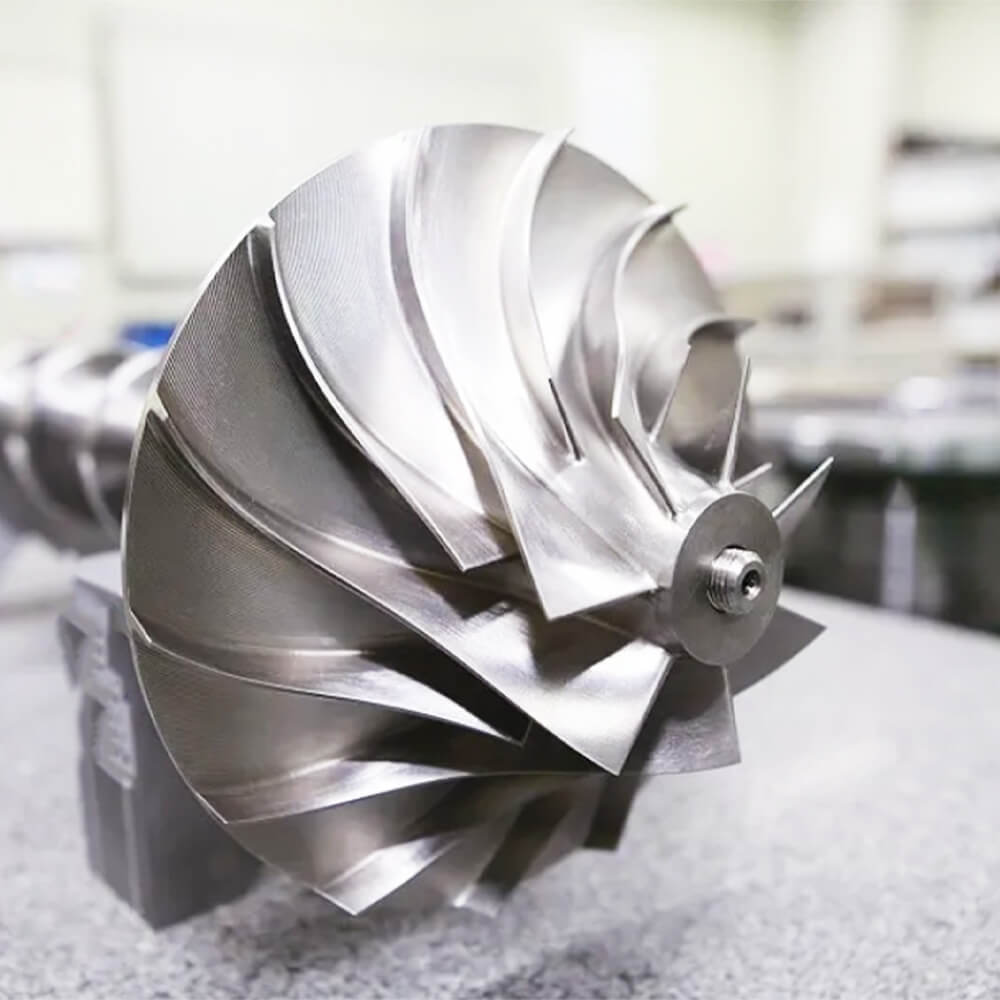
In the aerospace industry, 3D printing has been used to produce lightweight, high-strength parts for aircraft and spacecraft. 3D printing allows for the creation of intricate parts that are both strong and lightweight, reducing the weight of aircraft and spacecraft and improving their performance. This is particularly important in the aerospace industry, where every gram of weight saved can have a significant impact on fuel efficiency and range.
In the automotive industry, 3D printing has been used to produce everything from small brackets and clips to entire car bodies. For example, Bugatti used 3D printing to produce the titanium brake caliper for their Chiron supercar, which is not only lighter but also stronger than a traditional cast caliper. Audi has used 3D printing to produce customized tail lights for their R8 sports car, while Porsche has used the technology to produce parts for their classic vehicles that are no longer in production.
One of the biggest advantages of using 3D printing to produce car parts is the ability to create customized parts on demand. This is particularly useful for producing replacement parts for older vehicles, where the original parts are no longer in production. With 3D printing, car enthusiasts can produce replacement parts that are identical to the original, ensuring that their classic cars remain in top condition.
Another advantage of 3D printing automotive parts is the ability to reduce waste and improve sustainability. With traditional manufacturing techniques, a significant amount of material is often wasted during the production process. With 3D printing, only the material required to produce the part is used, reducing waste, and improving efficiency. Additionally, 3D printing allows for the use of recycled materials, further reducing the environmental impact of manufacturing.
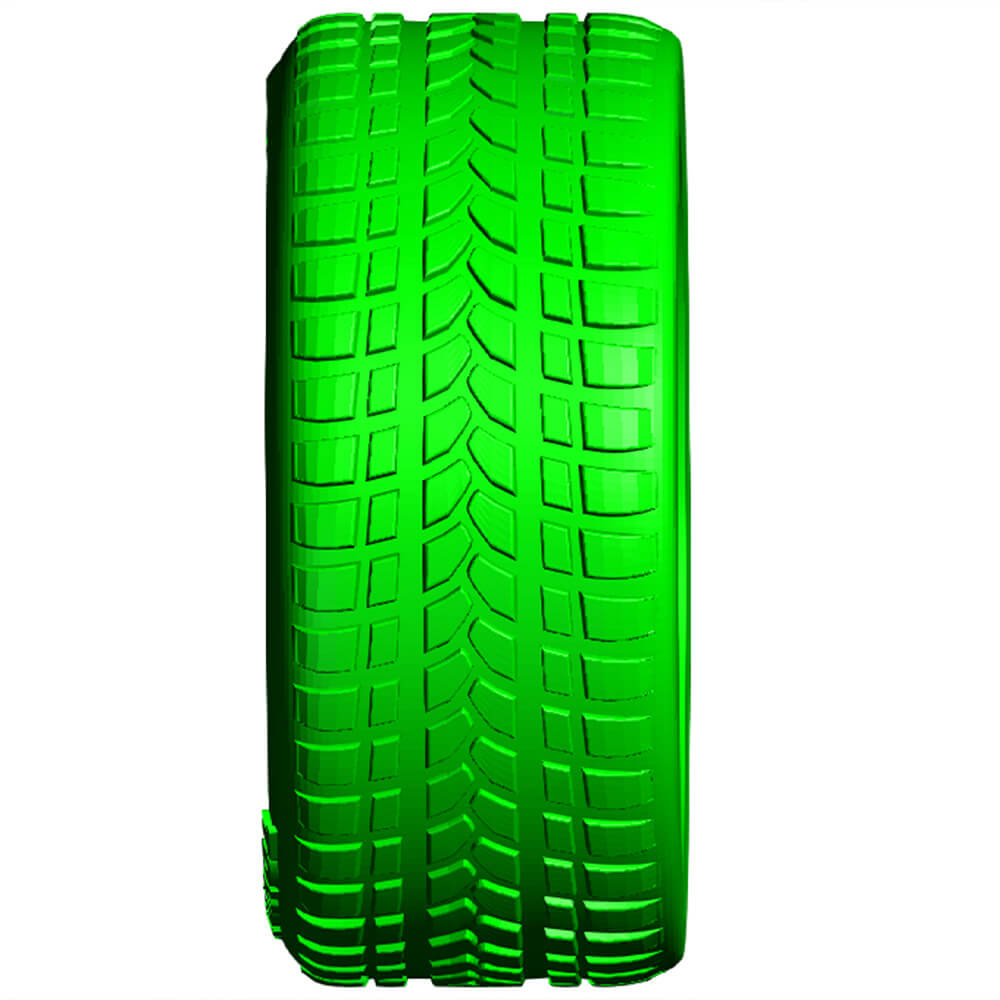
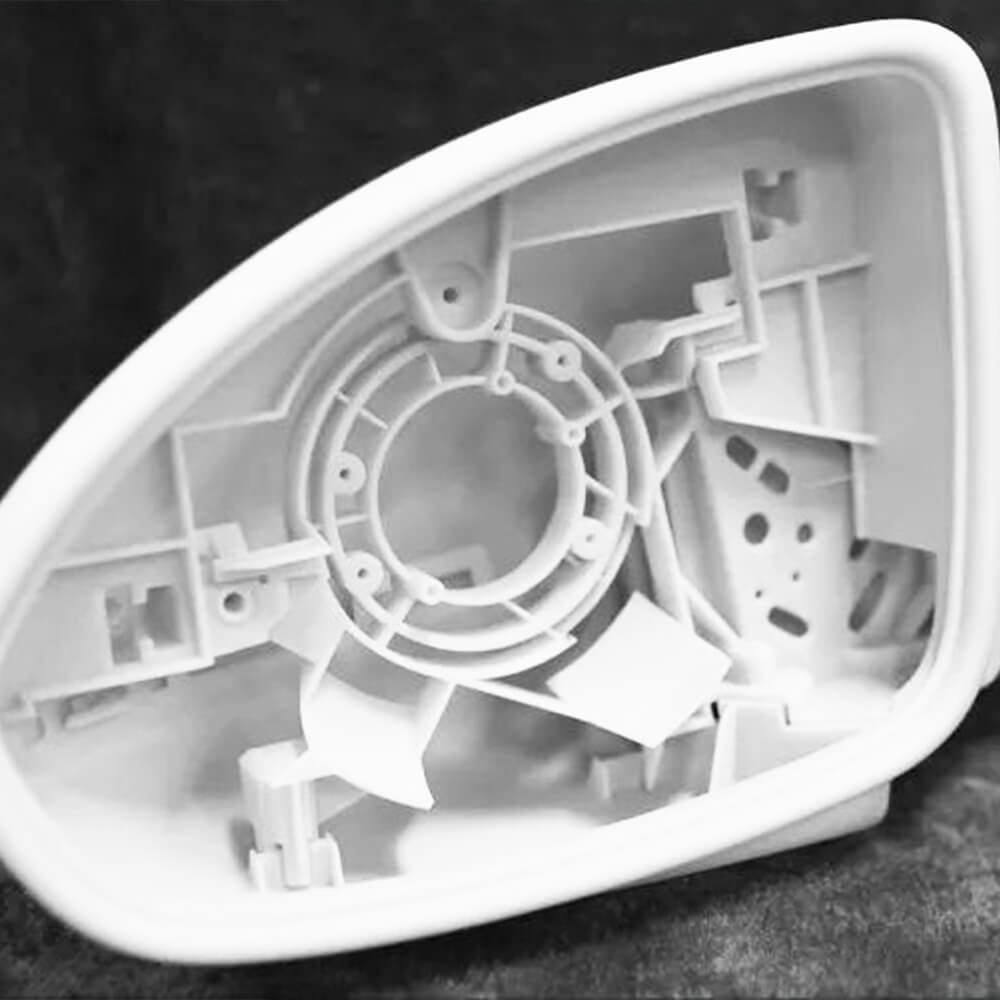
3D printing has had a significant impact on the automotive and aerospace industries, allowing to produce complex and customized parts that are both strong and lightweight. 3D printing has been used to produce everything from small brackets and clips to entire car bodies and has been particularly useful for producing replacement parts for older vehicles. With the ability to reduce waste and improve sustainability, 3D printing is likely to become an increasingly important technology in the automotive and aerospace industries in the years to come.